Do produkcji wykładzin MOHAWK najczęściej używane jest włókno poliamidowe (nylon) dlatego cały proces produkcji omówimy na przykładzie tego włókna.
Polimer do produkcji wykładzin (w tym wypadku poliamid), do fabryki produkującej włókno dostarczany jest w postaci granulatu. Cały proces produkcji włókna w uproszczeniu pokazuje schemat.
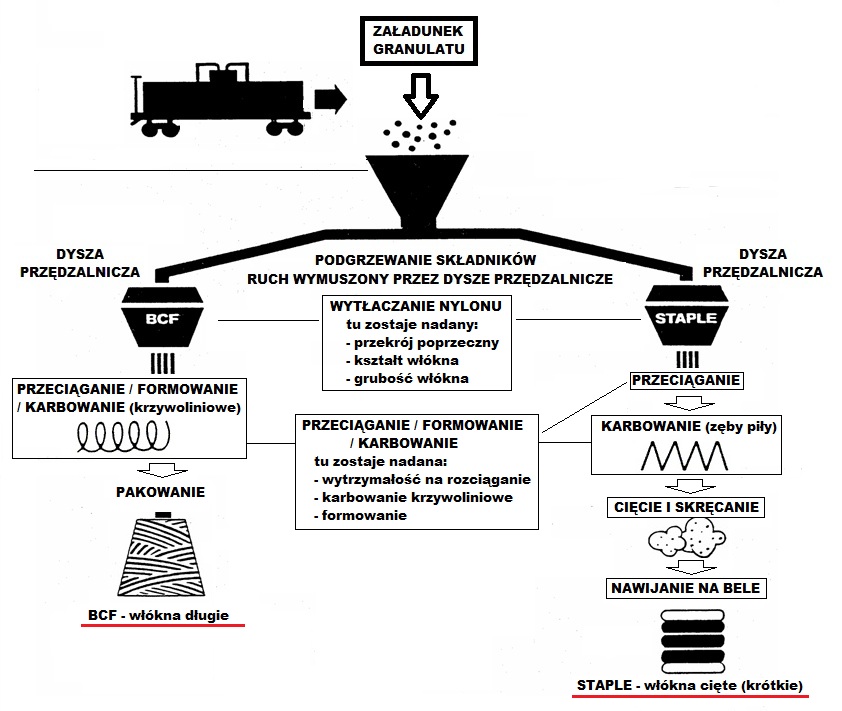
Włókna Staple są krótkie - mają 6-7 cali długości i po wytworzeniu muszą być połączone ze sobą w przędzę. Continuous Filament (BCF) to włókna długie, poskręcane, tworzące splot włókien. Te dwa różne procesy produkcj włókna dają przędzę o zróżnicowanym wyglądzie i charakterze.
Aby włókno mogło być użyte do produkcji dywanów lub wykładzin, musi przejść szereg procesów chemicznych oraz mechanicznych.
Żeby przybliżyć nieco temat wspomnimy o dwóch ważnych procesach w produkcji pokryć tekstylnych - barwienie włókna oraz jego skręcanie.
BARWIENIE
W najprostszy sposób mówiąc, jest to nadawanie wyprodukowanej przędzy lub wykładzinie potrzebnego koloru. Można tego dokonać na wiele sposobów, jednak dla uproszczenia przedstawimy trzy z nich.
Pierwszy to sposób powierzchniowego barwienia włókna, poprzez zanurzanie motków włókna w roztworze barwnika lub też, przez nanoszenie barwnika metodą drukarską - przy produkcji wykładzin drukowanych. Metoda ta jest powszechnie stosowana, a o skuteczności barwienia i trawłości kolorów decyduje zarówno jakość włókna jak i technologia barwienia.
Dokładnie tak samo można zabarwić już wyprodukowaną wykładzinę, umieszczając ją w specjalnych kadziach do barwienia. Ta metoda to barwienie kawałkami – w tej metodzie dywan jest barwiony razem z włóknami. Jest zanurzony w zbiorniku, zawieszony na dużych rolkach, które poruszają się razem z nim poprzez barwniki. Po barwieniu wykładzina jest wysuszona i poddawana dalszej obróbce.
Bardziej zaawansowaną technologią barwienia włókna jest tzw."barwienie w masie" lub "barwienie na wskroś".
Tutaj kolor "wplatany" jest w przędzę na etapie produkcji włókna. Jak pokazuje schemat - tzw. chipsy barwnika podawane są do dyszy przędzalniczej wraz z polimerem, z którego wytłaczane będzie właściwe włókno. W tym wypadku barwnik stanowi monolit z przędzą.
Takie włókno jest dużo bardziej odporne na wpływ zewnątrznych czynników takich jak światło i woda, a tym samym niedostrzegalna jest różnica koloru po długim okresie użytkowania wykładzin i częściowym ich "wytarciu". Wykładzina nie blaknie.
SKRĘCANIE
Na początku drogi rozwoju przemysłu dywanowego naturalne włókno podlegało tylko przędzeniu czyli nadawaniu jednolitego strumienia przędzy poprzez splatanie poszczególnych pojedynczych włókien. Z czasem wprowadzono także inne techniki splotu i skręcania, co wyrażnie poprawiło wytrzymałość oraz wygląd gotowego produktu.
Kolejnym etapem było dołączenie do procesu przędzenia tzw. nadmuchu powietrza, co w kapitalny sposób poprawiło puszystość przędzy, a co za tym idzie, gotowej wykładziny.
Jednym z ostatnich osiągnięć w dziedzinie produkcji włókna jest tzw. skręcanie na gorąco (heatsetting). Jest to proces, podczas którego nadaje się włóknom kształt spirali, w celu poprawienia sprężystości gotowego produktu. Cały cykl skręcania przebiega "na gorąco", a efektem tego zabiegu jest włókno, które najprościej mówiąc, ma "pamięć" kształtu i zdolnośc powrotu do formy pierwotnej. Ma to ogromne znaczenie dla użytkowania wykładzin, gdyż pozwala m.in. produktom o wysokim runie, na odzyskanie dawnego wyglądu po usunięciu obciążenia (np.meble), w wyniku którego powstało ugniecenie lub zadeptanie.
W przypadku skręcenia włókna bardzo duże znaczenie ma poziom skręcenia mierzony na długości cala (2,54 cm). Im bardziej skręcone włóno tym trudniej je wyprostować, tym lepiej zachowuje nadany mu kształt. Wykładziny z dużym poziomem skręcenia praktycznie dożywotnio zachowują strukturę.
Innym procesem w technologii powstawania wykładzin dywanowych jest zabezpieczenie włókna przed zabrudzeniem. Ten proces dokładnie omawiamy tutaj.
do góry